Introduction
Technip Energies has extensive expertise in ethylene and our design and technology know-how played a key role in the Reliance ethane project in India. Our part in the project involved the treatment of refinery off-gas to be used as single feedstocks for the ethane/propane cracker.
Providing expertise were our engineering centers in New Delhi, Mumbai and Chennai as well as our manufacturing facility in Dahej, Gujarat.
Challenge
A better valorization of this fuel gas was required.
Refinery off-gases are used as unique feedstock for ethylene plant
Two of the world’s largest refineries are located in Jamnagar, India and owned by Reliance. The refineries generate a large amount of fuel gas, which is conventionally burned in the refinery heaters.
A better valorization of this fuel gas is to produce hydrogen, ethylene and propylene.
The concept is based on direct recovery of the final products either from unsaturated gases from the fluid catalytic cracker (FCC) and coker or by cracking the recovered ethane, propane and C4 cut from saturated and unsaturated refinery off-gases from all units of the refinery.
Background
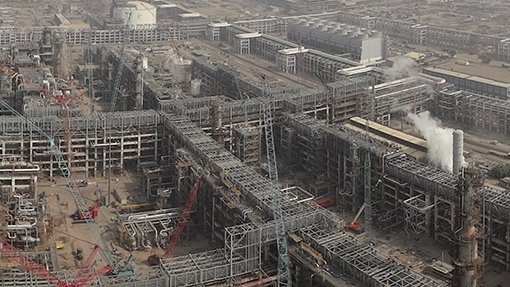
Depending on the crude type processed and the refinery units in operation, the quantity and quality of the fuel gases frequently vary. In addition, these fuel gases contain all kinds of impurities, including NOx, arsine, oxygen, sulfur compounds and ammonia, requiring dedicated treatments before they enter the steam cracker.
A complete survey of the two refineries was required to understand the variations in quality, quantity and impurities of the individual fuel gases. Having a map of these potential operation cases, Technip Energies performed various scenarios of operation.
As the quantity and quality of ethylene and propylene to be produced should be stable over the time, an additional fresh feedstock is required to compensate the large variations of the quantity of fuel gases arising from the operation of the refineries.
Solution
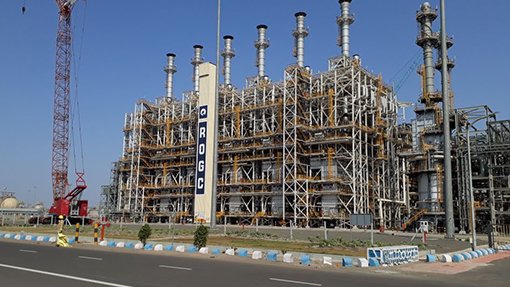
The Reliance refinery off-gases cracker is the first of its kind.
It is uncommon for an ethylene plant to use off-gases as the principal feedstock. With that in mind, Technip Energies developed a dedicated and innovative concept.
The concept is based on three processing trains with common facilities. Two dedicated processing trains are required for treatment and recovery of valuable products due to the different nature (composition and impurities) of saturated and unsaturated fuel gases. The third processing train corresponds to the cracker in which recovered ethane, propane and C4 cut are thermally cracked.
The common facilities between the trains are the refrigeration cycles, the C2 and C3 splitter for final purification of respectively ethylene and propylene, hydrogen purification and regeneration facilities for the multiple catalysts and absorbent beds required to remove the impurities. In case of shortage of refinery fuel gases used as fresh feedstock, propane is used as complementary feedstock to maintain the production of ethylene and propylene.
Results
The world’s only ethylene cracker with ROG as primary feed.
Technip Energies demonstrated its capability to design new concepts in full operation. The Reliance project contract from FEED to startup was signed in July 2012, the process units were started one by one in July 2017, and all performances guarantees were demonstrated and achieved in December 2017 with all units in operation. The plant is stable and all systems are working above capacity.
Cracking furnaces
kta Ethylene
kta Propylene
kta Hydrogen
Get in touch
Do you want to speak directly to our team?
You can browse our locations or send a message using the contact us form, both available on our Contact page.
- To discuss Reliance or similar projects, please select the Projects Asia-Pacific contact from the dropdown in the contact form.
General enquiries
For general queries, please use this field to send a message and we will direct it to the appropriate team.